Hyundai Ioniq: Dual Clutch Transmission Assembly / DCT (Dual Clutch Transmission). Repair procedures
•
| Be sure to read and follow the "General Safety Information and Caution" before doing any work related with the high voltage system. Failure to follow the safety instructions may result in serious electrical injuries. |
|
•
| Use fender covers to avoid damaging painted surfaces. |
•
| To avoid damage, unplug the wiring connectors carefully while holding the connector portion. |
|
1. | Shut off the High Voltage circuit. (Refer to General Information - "High Voltage Shutoff Procedure") |
2. | Remove the engine room under cover. (Refer to Engine And Transaxle Assembly - "Engine Room Under Cover") |
3. | Loosen the drain plug, and drain the inverter coolant. Remove the reservoir cap to help drain the coolant faster. (Refer to Hybrid Motor System - "Coolant") |
4. | Remove the HPCU (Hybrid Power Control Unit). (Refer to Hybrid Control System - "Hybrid Power Control Unit (HPCU)") |
5. | Remove the ECM (Engine Control Module) and TCM (Transmssion Control Module). (Refer to Engine Control/Fuel System - "Engine Control Module (ECM)") (Refer to Dual Clutch Control System - "DCT Control Module (TCM)") |
6. | Remove the HPCU (Hybrid Power Control Unit) tray. (Refer to Hybrid Control System - "Hybrid Power Control Unit (HPCU)") |
7. | Disconnect the gear actuator motor connector (A) and solenoid connector (B). 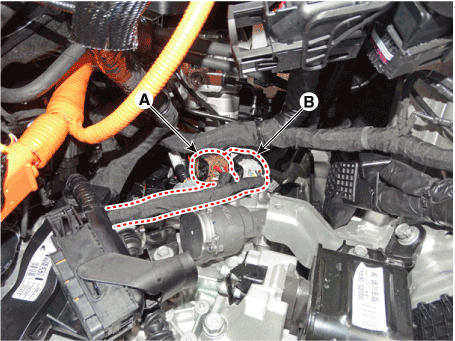
|
8. | Disconnect the hybrid motor connector (A) and engine clutch actuator connector (B). |
9. | Disconnect the DCT clutch actuator connector (C). 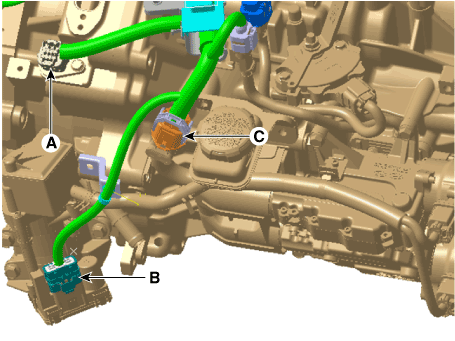
|
10. | Disconnect the inhibitor switch connector (A) and input shaft speed sensor connector (B). |
11. | Remove the ground bolt (C) and wiring bracket bolt (D). Tightening torque : 9.8 - 11.8 N.m (1.0 - 1.2kgf.m, 7.2 - 8.7 lb-ft) |
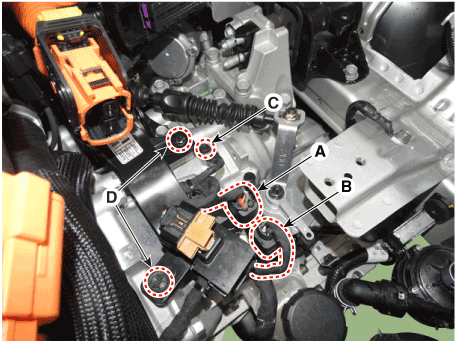
|
12. | Remove the nut (A) and shift cable bracket bolt (B-2ea). Tightening torque : (A) 9.8 - 13.7 N.m (1.0 - 1.4 kgf.m, 7.2 - 10.8 lb-ft) (B) 19.6 - 26.5 N.m (2.0 - 2.7 kgf.m, 14.5 - 19.5 lb-ft) |
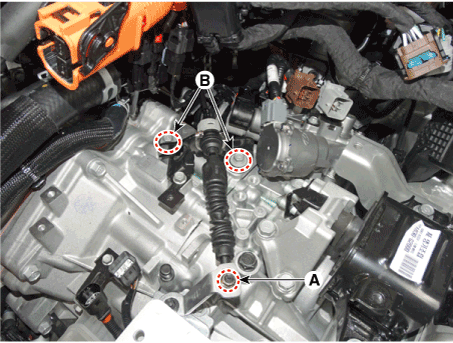
|
13. | Remove the ground bolts (A). 
|
14. | Remove the hybrid motor cooling hose (A). 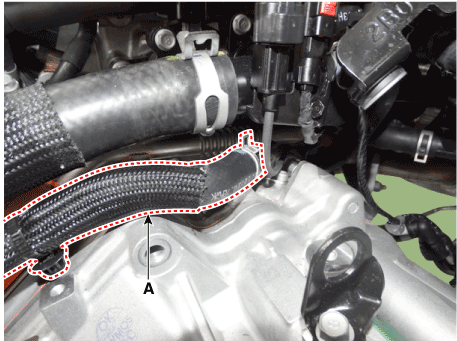
|
15. | Remove the hybrid motor upper mounting bolt (A-3ea). Tightening torque : 39.2 - 48.1 N.m (4.0 - 4.9kgf.m, 28.9 - 35.4 lb-ft) |
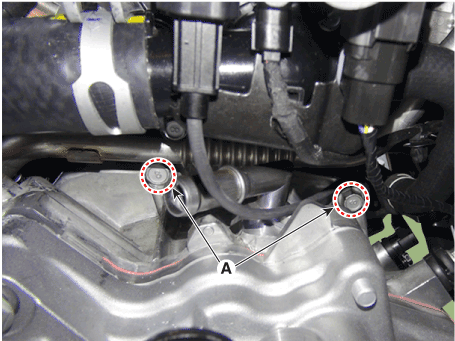
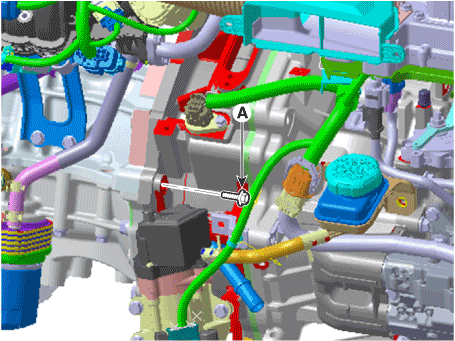
|
16. | Assemble the engine support fixture (beam No.: 09200-38001 or 09200-3N000, supporter No.: 09200-2S000). (Refer to Special Service Tools - "Engine Support Fixture Assembly Drawing") |
17. | Using the engine support fixture(A), hold the engine and transaxle assembly safely. 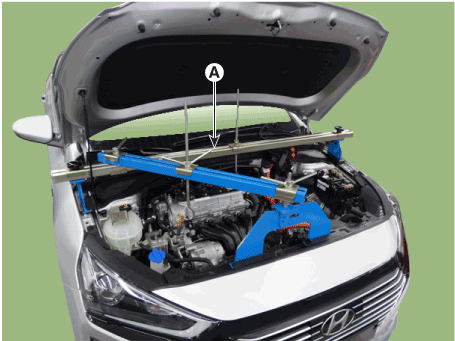
|
18. | Remove the dust cover (A). 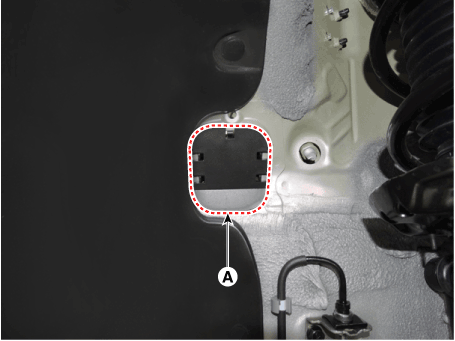
|
19. | Remove the transmission support bracket mounting bolt (A-2ea). Tightening torque : 88.3 - 107.9 N.m (9.0 - 11.0 kgf.m, 65.1 - 79.8 lb-ft) |
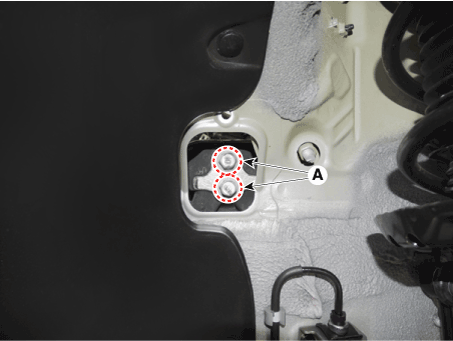
|
20. | Remove the transmission support bracket (A). Tightening torque : 58.8 - 78.5 N.m (6.0 - 8.0 kgf.m, 43.4 - 57.9 lb-ft) |
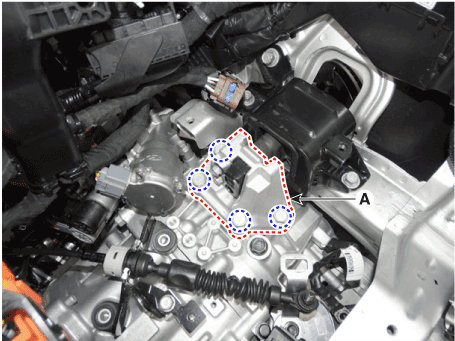
|
21. | Remove the sub frame. (Refer to Suspension System - "Sub Frame") |
22. | Remove the front drive shaft assembly. (Refer to Driveshaft and Axle - "Front Driveshaft") |
23. | Remove the AWEP (Auxiliary Electronic water pump). (Refer to Heating, Ventilation and Air Conditioning - "AWEP (Auxiliary Electronic water pump)") |
24. | Remove the crankshaft position sensor. (Engine Control / Fuel System - "Crankshaft Position Sensor (CKPS)") |
25. | Remove the roll rod support bracket (A). Tightening torque : 49.0 - 68.6 N.m (5.0 - 7.0 kgf.m, 36.2 - 50.6 lb-ft) |
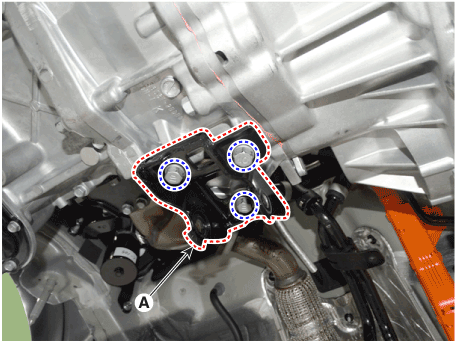
|
26. | Support the hybrid motor and transmission safely by using the jack. |
27. | Remove the hybird motor lower mounting bolts (A, B). Tightening torque : (A) 39.2 - 48.1 N.m (4.0 - 4.9kgf.m, 28.9 - 35.4 lb-ft) (B) 48.1 - 53.9 N.m (4.9 - 5.5kgf.m, 35.4 - 39.8 lb-ft) |
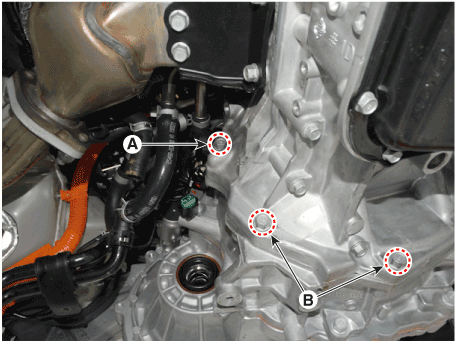
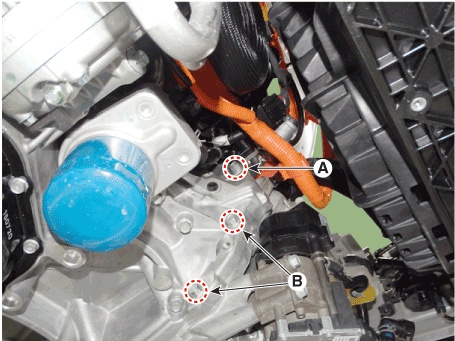
|
28. | After separating the hybrid motor and transmission from the engine, remove the transmission by lowering the jack slowly. •
| Be careful not to damage other system or parts near by when removing the hybrid motor and transmission assembly. |
|
|
29. | Remove the hybrid motor assembly from the dual clutch transmission. |
1. | Install in the reverse order of removal. Matters that require attention when installing the dual clutch transmission (DCT) to hybrid motor. 1) | Check the pilot bearing (A) and connector on the side of motor for any dents, damages and deformations before installing the DCT. 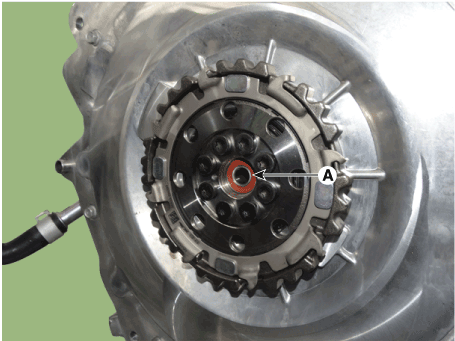
|
2) | Align the connector on the side of motor (A) with the dual clutch spline (B). 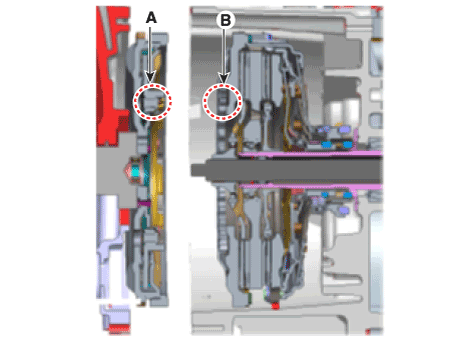
|
3) | Insert the input shaft (A) to the engine pilot bearing (B) and then assemble the DCT to the knock bushing on the hybrid motor side. 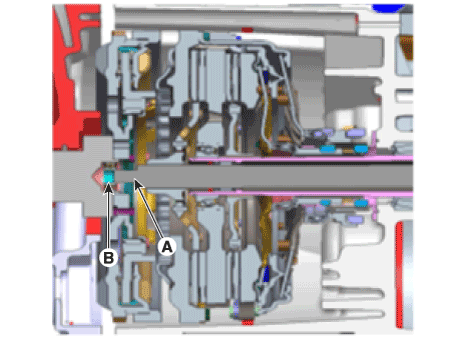
|
4) | After adhering the DCT with hybrid motor by pushing the DCT, tighten the mounting bolts after checking that there is no gap (less than 2mm) between the clutch housing and the hybrid motor housing. (If the bolt is tightened while there is a gap, then the spline of external damper or clutch will be damaged or broken.) 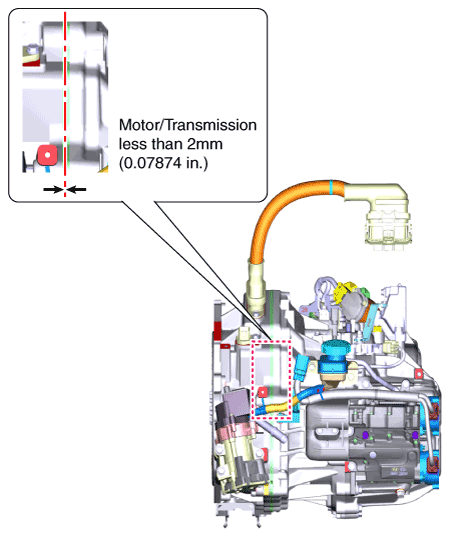
|
|
|
2. | Observe each separate procedure below for reinstallation or replacement with a new dual clutch transmission. |
When reinstalling
1. | If the differential oil seal is damaged and oil is leaking, replace the oil seal with a new one. When installing a new oil seal, use the special tool (09430-C1190, 09231-H1100). |
2. | After installing the DCT, check the oil level after refilling the DCT with oil. (Refer to Dual Clutch Transmission System - "Transmission Gear oil") |
3. | Bleed air from the hybrid motor cooling system using GDS. (Refer to Hybrid Motor System- "Coolant") |
4. | Clear the diagnostic trouble codes (DTC) using the KDS/GDS. Disconnecting the battery negative terminal will not clear the DTCs. Clear the DTCs using the KDS/GDS at all times. |
When replacing with a new dual clutch transmission
1. | After replacing the new DCT, it need not oil refill & level check procedure because oil is already filled with specified quantity inside new DCT. |
2. | Clear the diagnostic trouble codes (DTC) using the KDS/GDS. Disconnecting the battery negative terminal will not clear the DTCs. Clear the DTCs using the KDS/GDS at all times. |
3. | Bleed air from the hybrid motor cooling system using the GDS. (Refer to Hybrid Motor System- "Coolant") |
4. | Perform initialization of the engine clutch inspection line learning and diagnostic information using the GDS. 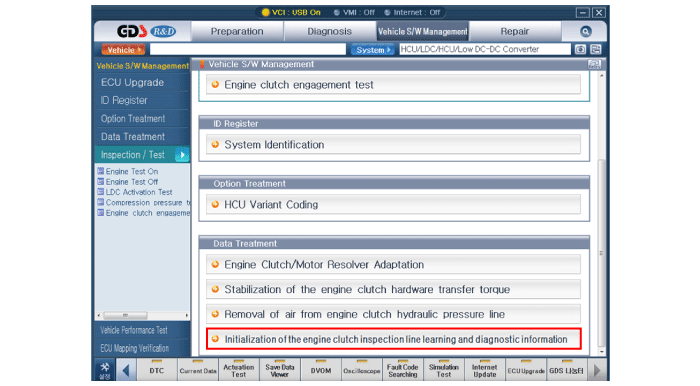
|
5. | Perform of the removal of air from engine clutch hydraulic pressure line using the GDS. 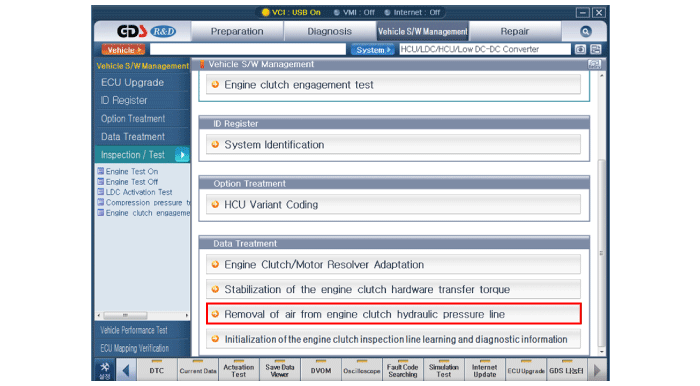
|
6. | Perform of the engine clutch/motor resolver adaptation using the GDS. 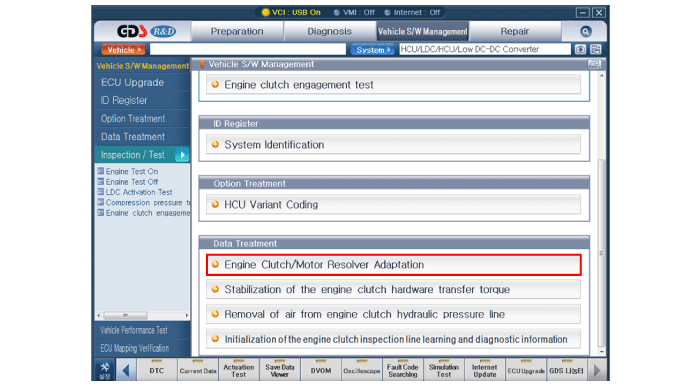
|
7. | Perform of the stabilization of the engine clutch hardware transfer torque using the GDS. 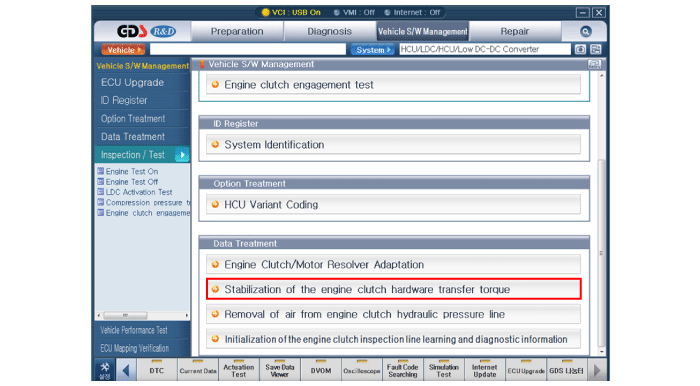
|
8. | Perform clutch characteristics input procedure using the GDS. (One of two procedures must be performed.) •
| Clutch characteristics input (Manual Teaching) 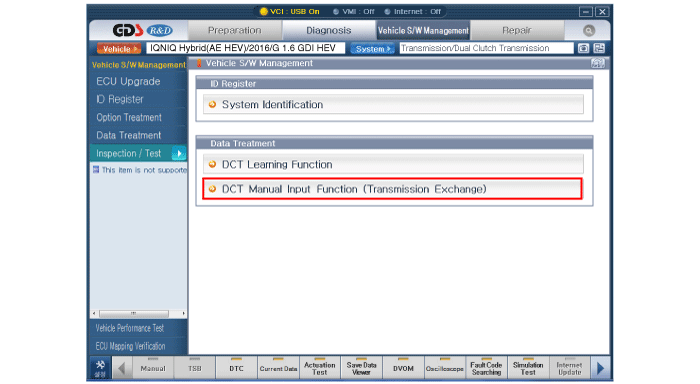
|
•
| Clutch touch point learning 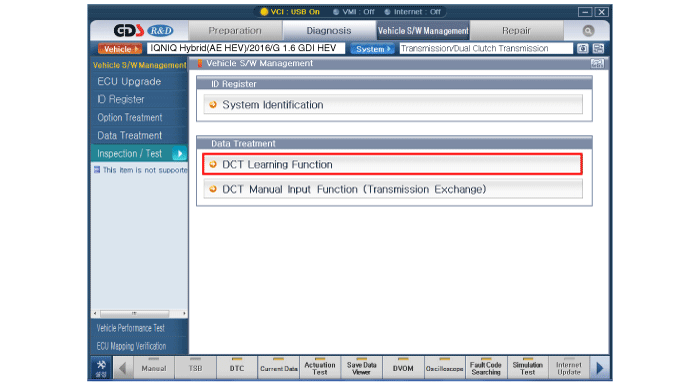
|
|
Components (1)1. Dual clutch transmission assembly2. Hybrid motor assembly3. Gear actuator4. Clutch actuator5. Engine clutch actuator6. Reserver7. Dust cover8...
General Information1.Check & Change intervals Check & Replenishment Change Capacity Oil specification Normal Use Severe Use No checkNo service required120000 km( 80000 miles)1...
Other information:
Filter Inspection
The climate control air filter should be replaced according to the Maintenance
Schedule. If the vehicle is operated in severely air-polluted cities or on dusty
rough roads for a long period, it should be inspected more frequently and replaced
earlier...
C..
Categories
Seat belt warning light
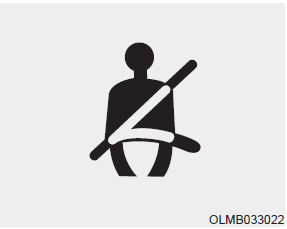
As a reminder to the driver, the seat belt warning light will illuminate and
warning chime will sound for approximately 6 seconds each time you place the Engine
Start/Stop button to the ON position if the seat belt is unfastened.
read more