Hyundai Ioniq: Engine Control/Fuel System / Troubleshooting
Basic Troubleshooting Guide
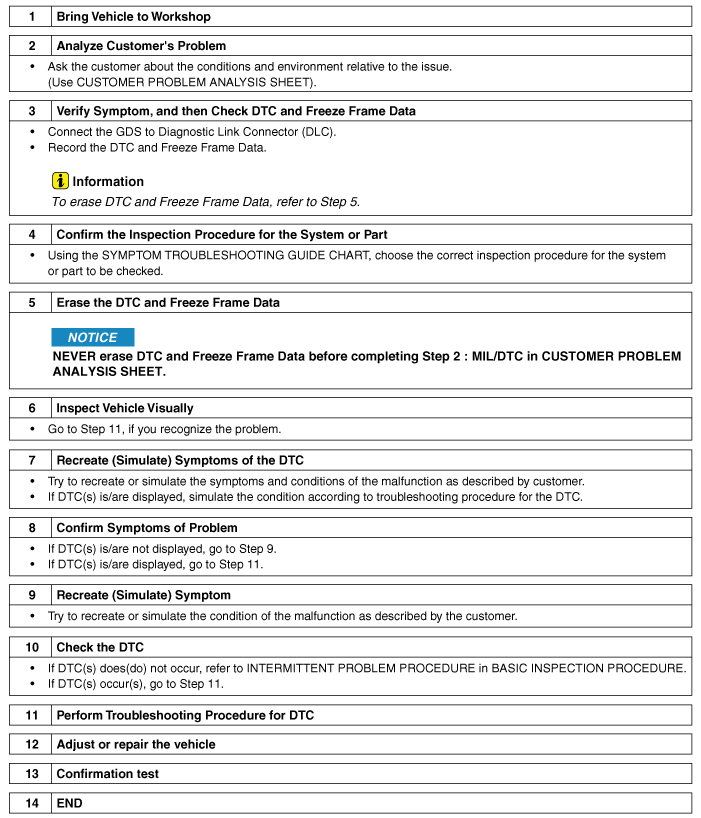
Customer Problem Analysis Sheet
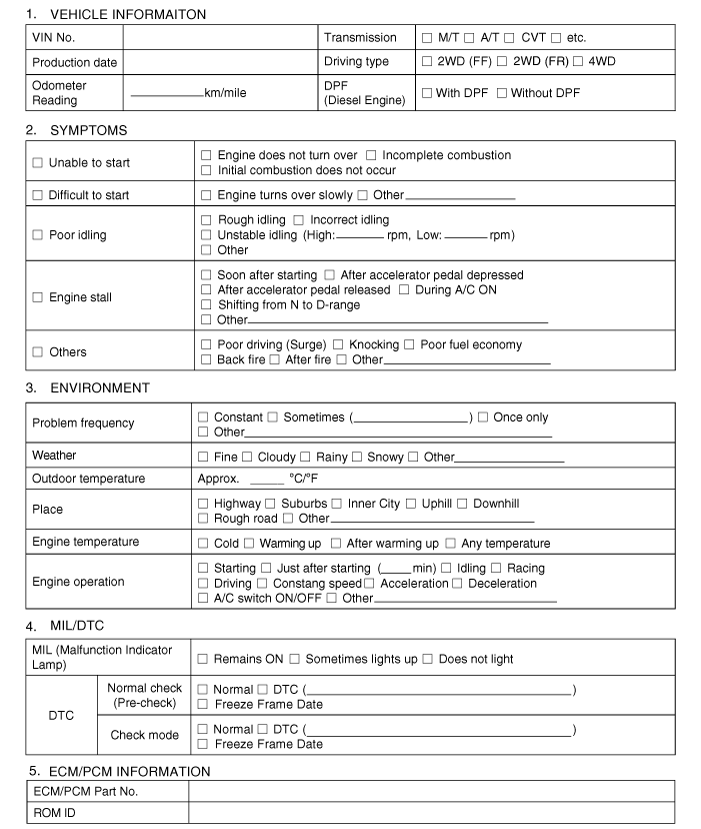
Basic Inspection Procedure
Measuring Condition of Electronic Parts' Resistance |
The measured resistance at high temperature after vehicle running may be high or low. So all resistance must be measured at ambient temperature (20°C, 68°F), unless stated otherwise.
•
| The measured resistance in except for ambient temperature (20°C, 68°F) is reference value. |
|
Intermittent Problem Inspection Procedure |
Sometimes the most difficult case in troubleshooting is when a problem symptom occurs but does not occur again during testing. An example would be if a problem appears only when the vehicle is cold but has not appeared when warm. In this case, the technician should thoroughly make out a "Customer Problem Analysis Sheet" and recreate (simulate) the environment and condition which occurred when the vehicle was having the issue.
1. | Clear Diagnostic Trouble Code (DTC). |
2. | Inspect connector connection, and check terminal for poor connections, loose wires, bent, broken or corroded pins, and then verify that the connectors are always securely fastened. 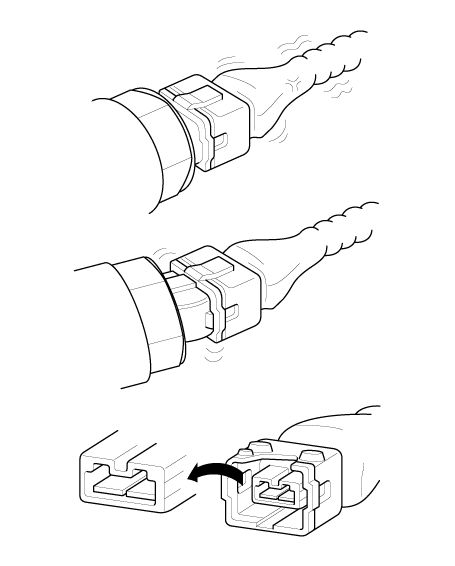
|
3. | Slightly shake the connector and wiring harness vertically and horizontally. |
4. | Repair or replace the component that has a problem. |
5. | Verify that the problem has disappeared with the road test. |
● Simulating Vibration
a. | Sensors and Actuators : Slightly vibrate sensors, actuators or relays with finger. •
| Strong vibration may break sensors, actuators or relays |
|
|
b. | Connectors and Harness : Lightly shake the connector and wiring harness vertically and then horizontally. |
● Simulating Heat
a. | Heat components suspected of causing the malfunction with a hair dryer or other heat source. •
| DO NOT heat components to the point where they may be damaged. |
•
| DO NOT heat the ECM directly. |
|
|
● Simulating Water Sprinkling
a. | Sprinkle water onto vehicle to simulate a rainy day or a high humidity condition. •
| DO NOT sprinkle water directly into the engine compartment or electronic components. |
|
|
● Simulating Electrical Load
a. | Turn on all electrical systems to simulate excessive electrical loads. (Radios, fans, lights, rear window defogger, etc.) |
Connector Inspection Procedure
1. | Handling of Connector a. | Never pull on the wiring harness when disconnecting connectors. 
|
b. | When removing the connector with a lock, press or pull locking lever. 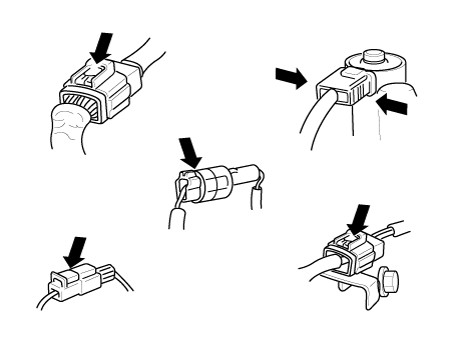
|
c. | Listen for a click when locking connectors. This sound indicates that they are securely locked. 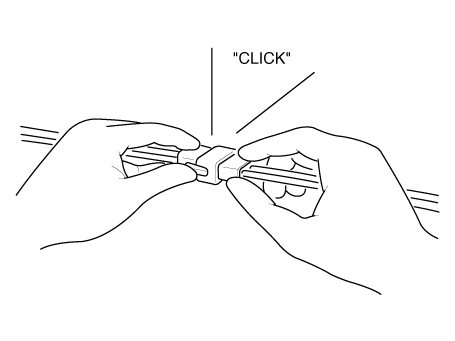
|
d. | When a tester is used to check for continuity, or to measure voltage, always insert tester probe from wire harness side. 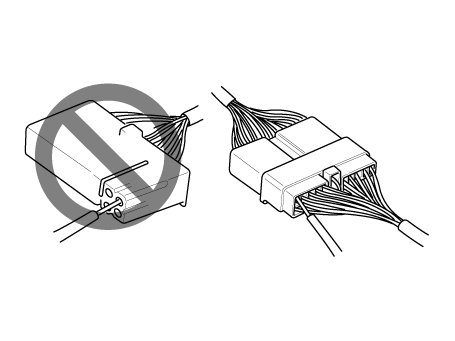
|
e. | Check waterproof connector terminals from the connector side. Waterproof connectors cannot be accessed from harness side. 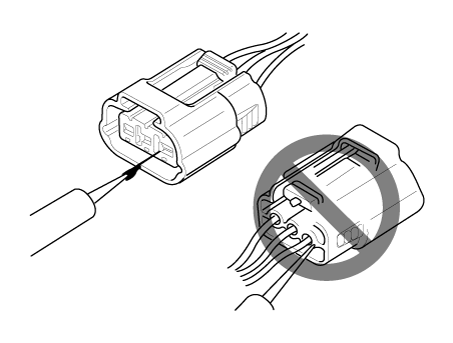
•
| Use a fine wire to prevent damage to the terminal. |
•
| Do not damage the terminal when inserting the tester lead. |
|
|
|
2. | Checking Point for Connector a. | While the connector is connected: Hold the connector, check connecting condition and locking efficiency. |
b. | When the connector is disconnected: Check missed terminal, crimped terminal or broken core wire by slightly pulling the wire harness. Visually check for rust, contamination, deformation and bend. |
c. | Check terminal tightening condition: Insert a spare male terminal into a female terminal, and then check terminal tightening conditions. |
d. | Pull lightly on individual wires to ensure that each wire is secured in the terminal. 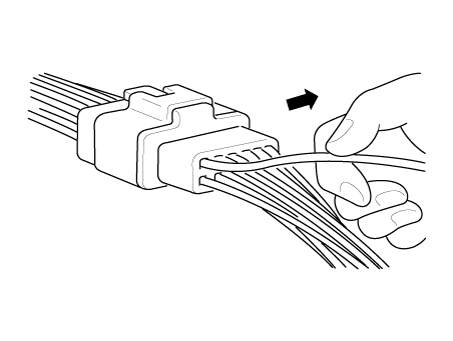
|
|
3. | Repair Method of Connector Terminal a. | Clean the contact points using air gun and/or shop rag. •
| Never use sand paper when polishing the contact points, otherwise the contact point may be damaged. |
|
|
b. | In case of abnormal contact pressure, replace the female terminal. |
|
Wire Harness Inspection Procedure
1. | Before removing the wire harness, check the wire harness position and crimping in order to restore it correctly. |
2. | Check whether the wire harness is twisted, pulled or loosened. |
3. | Check whether the temperature of the wire harness is abnormally high. |
4. | Check whether the wire harness is rotating, moving or vibrating against the sharp edge of a part. |
5. | Check the connection between the wire harness and any installed part. |
6. | If the covering of wire harness is damaged; secure, repair or replace the harness. |
Electrical Circuit Inspection Procedure
1. | Procedures for Open Circuit If an open circuit occurs (as seen in [FIG. 1]), it can be found by performing Step 2 (Continuity Check Method) or Step 3 (Voltage Check Method) as shown below. 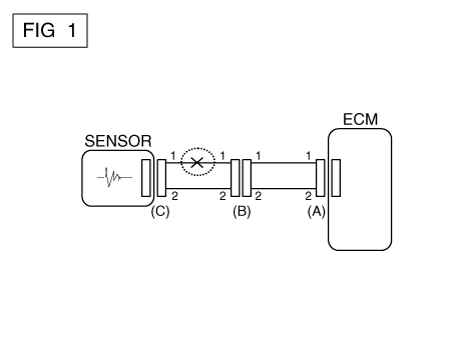
|
2. | Continuity Check Method •
| When measuring for resistance, lightly shake the wire harness above and below or from side to side. |
|
Specification (Resistance) 1Ω or less → Normal Circuit 1MΩ or Higher → Open Circuit |
a. | Disconnect connectors (A), (C) and measure resistance between connector (A) and (C) as shown in [FIG. 2]. In [FIG.2.] the measured resistance of line 1 and 2 is higher than 1kΩ and below 1Ω respectively. Specifically the open circuit is line 1 (Line 2 is normal). To find exact break point, check sub line of line 1 as described in next step. 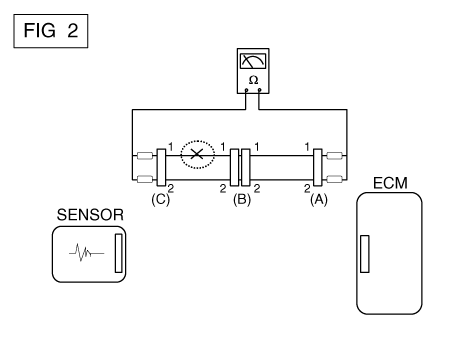
|
b. | Disconnect connector (B), and measure for resistance between connector (C) and (B1) and between (B2) and (A) as shown in [FIG. 3]. In this case the measured resistance between connector (C) and (B1) is higher than 1MΩ and the open circuit is between terminal 1 of connector (C) and terminal 1 of connector (B1). 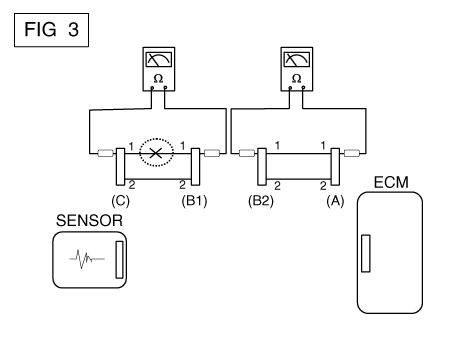
|
|
3. | Voltage Check Method a. | With each connector still connected, measure the voltage between the chassis ground and terminal 1 of each connectors (A), (B) and (C) as shown in [FIG. 4]. The measured voltage of each connector is 5V, 5V and 0V respectively. So the open circuit is between connector (C) and (B). 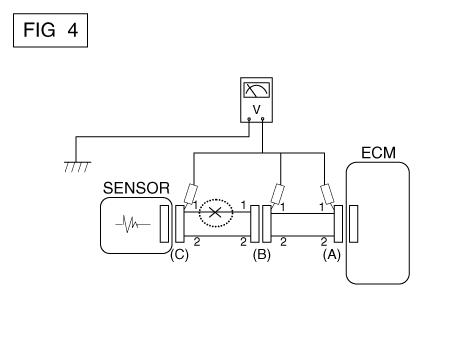
|
|
1. | Test Method for Short to Ground Circuit •
| Continuity Check with Chassis Ground |
If short to ground circuit occurs as shown in [FIG. 5], the broken point can be found by performing Step 2 (Continuity Check Method with Chassis Ground) as shown below. 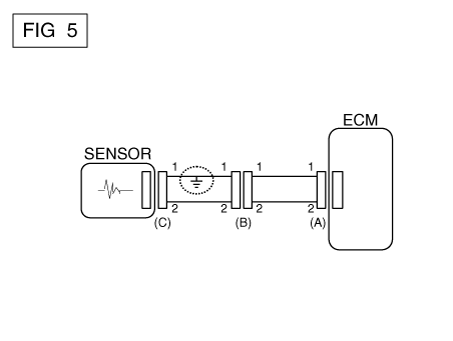
|
2. | Continuity Check Method (with Chassis Ground) •
| Lightly shake the wire harness above and below, or from side to side when measuring the resistance. |
|
Specification (Resistance) 1Ω or less → Short to Ground Circuit 1MΩ or Higher → Normal Circuit |
a. | Disconnect connectors (A), (C) and measure for resistance between connector (A) and Chassis Ground as shown in [FIG. 6]. The measured resistance of line 1 and 2 in this example is below 1Ω and higher than 1MΩ respectively. Specifically the short to ground circuit is line 1 (Line 2 is normal). To find exact broken point, check the sub line of line 1 as described in the following step. 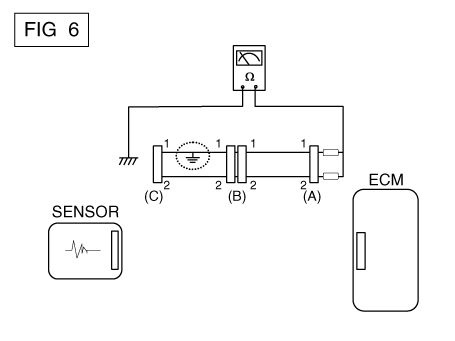
|
b. | Disconnect connector (B), and measure the resistance between connector (A) and chassis ground, and between (B1) and chassis ground as shown in [FIG. 7]. The measured resistance between connector (B1) and chassis ground is 1Ω or less. The short to ground circuit is between terminal 1 of connector (C) and terminal 1 of connector (B1). 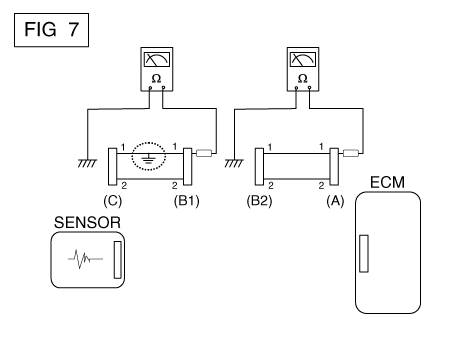
|
|
● Testing For Voltage Drop |
This test checks for voltage drop along a wire, or through a connection orswitch.
A. | Connect the positive lead of a voltmeter to the end of the wire (or to the side of the connector or switch) closest to the battery. |
B. | Connect the negative lead to the other end of the wire. (or the other side of the connector or switch) |
D. | The voltmeter will show the difference in voltage between the two points. A difference, or drop of more than 0.1 volts (50 mV in 5V circuits), may indicate a problem. Check the circuit for loose or dirty connections. |
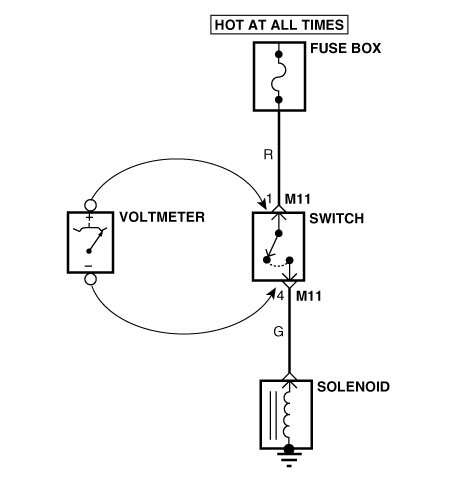
Symptom Troubleshooting Guide Chart
Main symptom
| Diagnostic procedure
| Also check for
|
Unable to start (Engine does not turn over)
| 1) | Test the battery. (Refer to Engine Electrical System - "Battery") |
2) | Test the starter. (Refer to Engine Electrical System - "Starter") |
3) | Inhibitor switch (A/T) or clutch start switch (M/T) |
|
|
Unable to start (Incomplete combustion)
| 1) | Test the battery. (Refer to Engine Electrical System - "Battery") |
2) | Check the fuel pressure (Refer to Fuel Delivery System - "Fuel Pressure Test") |
3) | Check the ignition circuit. (Refer to Engine Electrical System - "Ignition System") |
4) | Troubleshooting the immobilizer system. (Refer to Body Electrical System - "Immobilizer System") (In case of immobilizer lamp flashing) |
| •
| Slipped or broken timing belt |
|
Difficult to start
| 1) | Test the battery. (Refer to Engine Electrical System - "Battery") |
2) | Check the fuel pressure (Refer to Fuel Delivery System - "Fuel Pressure Test") |
3) | Check the ECT sensor and circuit (Check DTC) |
4) | Check the ignition circuit. (Refer to Engine Electrical System - "Ignition System") |
| |
Poor idling (Rough, unstable or incorrect Idle)
| 1) | Check the fuel pressure. (Refer to Fuel Delivery System - "Fuel Pressure Test") |
2) | Check the Injector. (Refer to Engine Control System - "Injector") |
3) | Check the long term fuel trim and short term fuel trim (Refer to CUSTOMER DATASTREAM) |
4) | Check the idle speed control circuit (Check DTC) |
5) | Inspect and test the Throttle Body |
6) | Check the ECT sensor and circuit (Check DTC) |
| |
Engine stall
| 1) | Test the battery. (Refer to Engine Electrical System - "Battery") |
2) | Check the fuel pressure. (Refer to Fuel Delivery System - "Fuel Pressure Test") |
3) | Check the idle speed control circuit (Check DTC) |
4) | Check the ignition circuit. (Refer to Engine Electrical System - "Ignition System") |
5) | Check the CKPS Circuit (Check DTC) |
| |
Poor driving (Surge)
| 1) | Check the fuel pressure. (Refer to Fuel Delivery System - "Fuel Pressure Test") |
2) | Inspect and test Throttle Body |
3) | Check the ignition circuit. (Refer to Engine Electrical System - "Ignition System") |
4) | Check the ECT Sensor and Circuit (Check DTC) |
5) | Test the exhaust system for a possible restriction. (Refer to Engine Mechanical System - "Exhaust Manifold") |
6) | Check the long term fuel trim and short term fuel trim (Refer to CUSTOMER DATASTREAM) |
| |
Knocking
| 1) | Check the fuel pressure. (Refer to Fuel Delivery System - "Fuel Pressure Test") |
2) | Inspect the engine coolant. (Refer to Engine Mechanical System - "Radiator") |
3) | Inspect the radiator and the electric cooling fan. (Refer to Engine Mechanical System - "Radiator") |
4) | Check the spark plugs. (Refer to Engine Electrical System - "Ignition System") |
| |
Poor fuel economy
| 1) | Check customer's driving habitsIs · A/C on full time or the defroster mode on? · Are tires at correct pressure? · Is excessively heavy load being carried? · Is acceleration too much, too often? |
2) | Check the fuel pressure. (Refer to Fuel Delivery System - "Fuel Pressure Test") |
3) | Check the injector. (Refer to Engine Control System - "Injector") |
4) | Test the exhaust system for a possible restriction |
5) | Check the ECT sensor and circuit |
| |
Hard to refuel (Overflow during refueling)
| 1) | Inspect the fuel filler hose/pipe · Pinched, kinked or blocked? · Filler hose is torn |
2) | Inspect the fuel tank vapor vent hose between the EVAP. canister and air filter |
3) | Check the EVAP. canister |
| •
| Malfunctioning gas station filling nozzle (If this problem occurs at a specific gas station during refueling) |
|
Special Service Tools
Item
Illustration
Application
Fuel Pressure Gauge(09353-24100)Measuring the fuel line pressureFuel Pressure Gauge Adapter(09353-02100)Connection between the high pressure fuel pump and the fuel feed lineHeated Oxygen Sensor Socket Wrench(09392-1Y100)Removal and installation of the heated oxygen sensor※ SST No...
Other information:
Components[RADIO/CD/MP3]Connector Pin Information
No
Connector A
Connector B
1Rear speaker (LH +)-2Rear speaker (LH -)Mic (+)3--4--5-Antenna power6Camera powerIllumination (+)7Camera vidio inputMM CAN (+)8--9--10-Battery (+)11DTCBattery (+)12Steering key signalGround13Front speaker (LH +)Ground14Front speaker (LH -)-15Front speaker (RH -)Mic (-)16Front speaker (RH +)-17--18- -19-Illumination (-)20Camera power groundMM CAN (-)21Camera video ground-22-ACC23--24--25--26Steering key ground-27Rear speaker (RH -)-28Rear speaker (RH +)-29--30--31-IGN 332Camera(NC...
C..
Categories
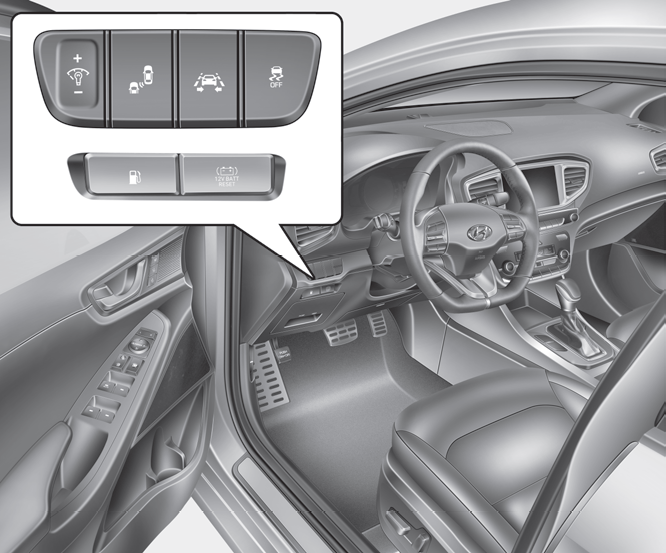
1. Door lock/unlock button
2. Driver position memory system
3. Side view mirror control switch
4. Central door lock switch
read more